Maximizing Oil Production Efficiency: Reducing Downtime and Boosting Productivity in the Permian Basin with OPTAC-X
- Dr. Patrick Fullerton
- Feb 22
- 4 min read
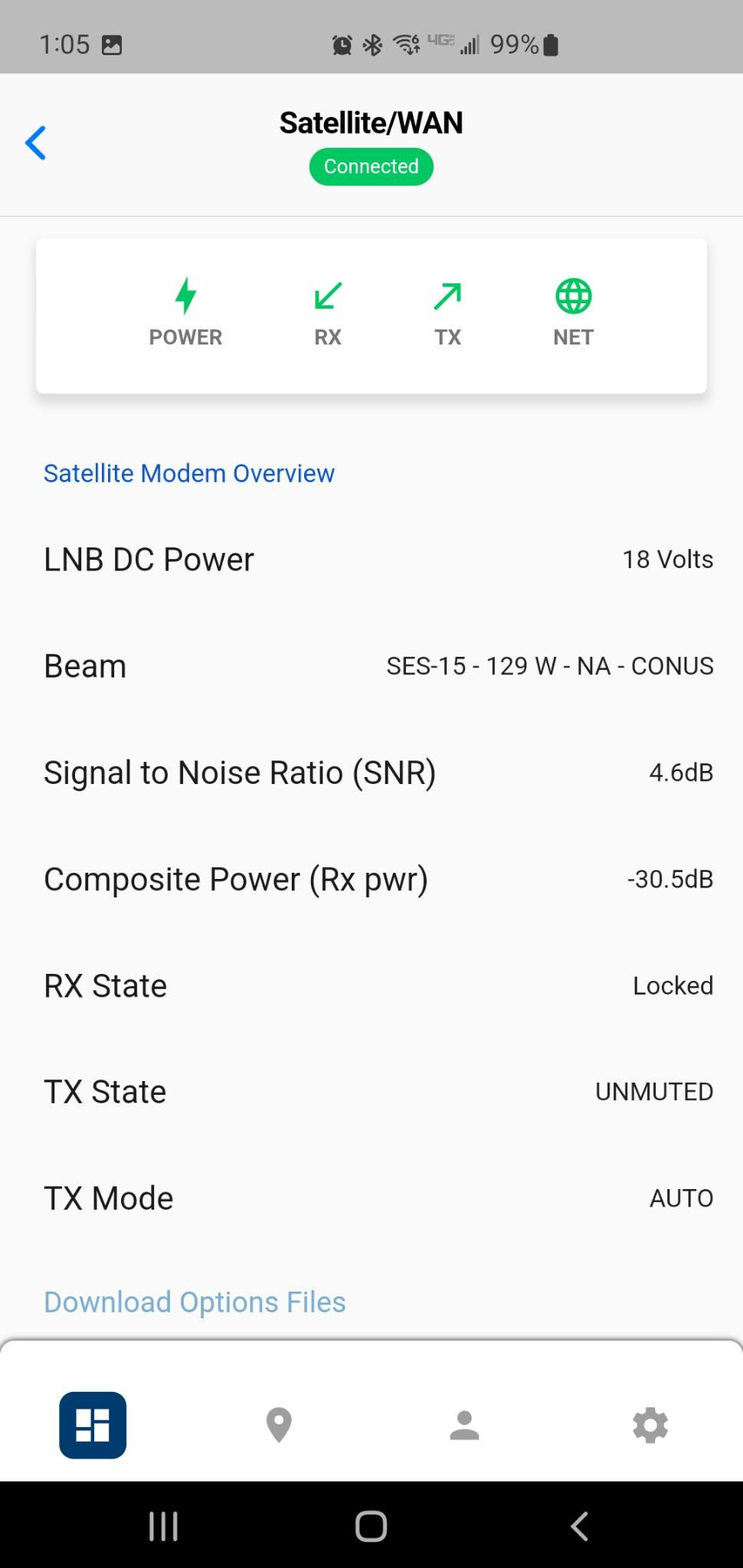
Revolutionizing Oil and Gas Maintenance in the Permian Basin: The Power of Preventative Maintenance with OPTAC-X
Introduction
Tele-preventative maintenance (tele-PM) leverages remote monitoring, diagnostics, and predictive analytics to streamline maintenance operations in the oil and gas sector. By integrating OPTAC-X technology, companies like ExxonMobil, Chevron, and Diamondback Energy operating in the Permian Basin can experience cost savings and increased productivity through reduced downtime, extended equipment lifespans, and optimized resource allocation.
Benefits of Tele-Preventative Maintenance
1. Reduced Downtime Remote monitoring enables the early detection of equipment anomalies, preventing catastrophic failures and unplanned shutdowns. For example, ExxonMobil can deploy OPTAC-X to monitor pump integrity in real-time, allowing rapid intervention before equipment fails.
2. Cost Savings Tele-PM reduces the frequency and cost of on-site inspections by deploying predictive analytics to identify when maintenance is required. Chevron could reduce expenditures by using OPTAC-X's data-driven approach, avoiding unnecessary field visits.
3. Increased Equipment Lifespan Consistent monitoring and timely intervention can extend the operational life of machinery. Diamondback Energy can benefit by avoiding accelerated wear and tear on its drilling rigs.
4. Enhanced Productivity Continuous real-time diagnostics mean faster decision-making and improved scheduling of maintenance activities. This is critical in the Permian Basin, where operational efficiency directly impacts production output.
Examples of Tele-PM in Action
ExxonMobil
ExxonMobil's vast infrastructure in the Permian Basin can benefit from OPTAC-X by detecting early warning signs of compressor issues. Remote telemetry could prevent equipment from failing mid-operation, saving millions in unplanned shutdown costs and enhancing production uptime. Savings Example: Compressor repairs can cost upwards of $250,000 per unit. Early detection through tele-PM could reduce costs by 40% annually.
Chevron
Chevron operates multiple pipelines and pumping stations across the Permian Basin. By integrating OPTAC-X, pipeline corrosion or leaks can be detected remotely. Automated diagnostics could dispatch maintenance teams precisely where needed, avoiding costly environmental fines and production loss. Productivity Example: An optimized pipeline inspection process can cut response times by 50%, improving operational output by 15%.
Diamondback Energy
Diamondback Energy With its focus on fracking operations, Diamondback Energy could leverage OPTAC-X to monitor high-pressure pumps. Predictive analytics could notify engineers of imminent failures, preventing costly downtime and enhancing fracking efficiency. Efficiency Example: Tele-PM can extend the operational hours of high-pressure pumps by 20%, saving $500,000 annually in reduced wear and tear.
How It Saves Money
Labor Costs: Fewer on-site inspections mean reduced labor requirements and travel expenses.
Environmental Compliance: Early detection of leaks and emissions reduces the risk of regulatory fines.
Energy Costs: Optimized equipment usage lowers energy consumption during operations.
How It Increases Productivity
Real-Time Insights: Access to live operational data reduces decision-making delays.
Automated Alerts: Maintenance crews are deployed only when necessary, minimizing disruptions.
Optimized Resources: Efficient allocation of tools, parts, and personnel ensures seamless operations.
Downtime in the Oil and Gas Industry
Industry-Wide Downtime Costs
Unplanned downtime remains a major cost driver in the oil and gas industry, averaging $149 million per site in 2024. Predictive maintenance strategies are increasingly adopted to detect anomalies early and prevent catastrophic failures.
Source: Innovapptive. (2024). Challenges of oil & gas equipment maintenance. Retrieved from https://www.innovapptive.com
Company-Specific Insights
Chevron: In Q2 2024, Chevron reported earnings below Wall Street estimates, attributing the shortfall to both unplanned and planned operational downtimes, particularly in its refining segment. Source: MarketWatch. (2024). Chevron reports Q2 earnings miss on weak refining margins. Retrieved from https://www.marketwatch.com
ExxonMobil: While specific downtime figures for 2024 are not disclosed, ExxonMobil's Q3 2024 report highlights a focus on operational excellence and cost efficiency, suggesting efforts to mitigate downtime impacts. Source: Oil & Gas Leads. (2024). ExxonMobil Q3 2024 highlights: Record performance in the Permian and upstream cost efficiency initiatives. Retrieved from https://oilgasleads.com
Diamondback Energy: In Q3 2024, Diamondback reported average production of 321.1 thousand barrels of oil per day (MBO/d). Although specific downtime data isn't provided, maintaining such production levels indicates effective management of operational interruptions. Source: Energy Analytics Institute. (2024). Diamondback reports Q3 2024 results; Updates on Endeavor deal. Retrieved from https://energy-analytics-institute.org
Tele-Preventative Maintenance and Connectivity Challenges
Cell Phone Service in the Permian Basin
Cellular service in the Permian Basin is often inconsistent due to:
Sparse Coverage: Limited cell towers in remote areas result in unreliable service.
Network Congestion: Increased worker presence during peak production can overload networks.
Environmental Challenges: Harsh weather and terrain can disrupt cell tower operations.
Value of OPTAC-X Communication Infrastructure (LTE/SATCOM)
1. Reliable Communication: Private LTE networks and satellite communications ensure connectivity in remote areas, enabling seamless operations.
2. Increased Operational Efficiency: Continuous communication between field equipment and monitoring centers allows for early detection of potential issues, reducing unplanned downtime.
3. Enhanced Safety: Reliable communication ensures swift emergency responses and real-time monitoring of worker safety.
4. Cost Savings: Better communication minimizes production interruptions and reduces logistics costs by enabling remote diagnostics.
5. Scalability for Future Needs: Supports IoT devices and automation technologies for future advancements.
Conclusion
By implementing tele-PM with OPTAC-X, oil and gas operators can significantly cut costs, enhance productivity, and improve safety, ensuring sustained operations and profitability in the competitive Permian Basin landscape.
Bibliography
Federal Communications Commission (FCC). (2023). Mobile Broadband Coverage in the United States. Retrieved from https://www.fcc.gov
RootMetrics. (2024). Wireless Network Performance in Rural Areas: Insights on Connectivity Challenges. Retrieved from https://www.rootmetrics.com
Permian Basin Petroleum Association (PBPA). (2024). Communication Challenges in the Permian Basin: A Case Study. Retrieved from https://pbpa.info
Oil & Gas Journal. (2024). Technology Solutions for Enhancing Safety and Efficiency in Oilfields. Retrieved from https://www.ogj.com
Innovapptive. (2024). The Role of IoT and Satellite Communications in Remote Oilfield Operations. Retrieved from https://www.innovapptive.com
OPTAC-X Technology Overview. (2024). Advancing Communication Infrastructure for Remote Operations. Internal White Paper.
Satellite Today. (2023). The Growing Role of SATCOM in Oil and Gas Operations. Retrieved from https://www.satellitetoday.com
Verizon Business. (2023). Private LTE for Oil and Gas: Transforming Remote Operations. Retrieved from https://www.verizon.com/business
Comments